PREVENTATIVE MAINTENANCE
Northeast Tech Compaction offers Preventative Maintenance programs that can help your operation reduce delays in productivity due to unexpected service repairs, prolongs the life and quality of your equipment, and improves employee safety. By taking a proactive approach our customers keep their equipment in top working condition. Speak to one of our representatives on how a preventative maintenance program can benefit your business'.
How would you like to reduce your recycling costs and increase your productivity? Northeast Tech Compaction can help! NTC's preventative maintenance programs are a cost effective way to extend the life of your recycling system.
Compactor and baler parts begin to wear over time. As they wear and parts become weak this leads to component failure and eventually downtime in productivity or even worse, sanitation issues. Equipment repairs and down time equals loss of profit. Performing regular maintenance helps you to achieve a productive and safe working environment for your employees.
Preventative maintenance is the only guaranteed solution that keeps equipment operating reliably, reduces repair costs, and maintains a safe working environment.
Our Preventative Maintenance programs:
-
Evaluate equipment condition.
-
Verify that all safety decals are in good condition.
-
Test and verify the operation of safety features.
-
Thoroughly inspect the welds and seals.
-
Grease all fittings.
-
Inspect all hoses and crimps.
-
Inspect all hose clamps and tighten as needed.
-
Inspect motor for signs of wear or end of life conditions.
-
Inspect pump for leaks or signs of failure.
-
Inspect oil level and general condition.
-
Operate gauge and verify that there are no leaks..
-
Set all Pressures.
-
Adjust Limit Switches as required.
-
Inspect ram or platen guide systems.
-
Inspect all control box switches and verify all are operational.
-
Inspect motor starter.
-
Inspect motor starter overload.
-
Inspect and test Emergency Stop Switches.
-
Inspect all electrical connections and tighten as needed.
-
Inspect wiring for signs of damage.
-
Perform structural inspection of equipment.
-
Verify that all safety covers are secure and properly positioned.
-
Inspect all loading doors and related safety switches.
-
Provide training to personnel on site during visit.
-
Verify area near equipment is clear of debris or improperly stored material.
-
All deficiencies communicated and solutions discussed.
We offer custom programs that may include:
-
Replacing of Hydraulic Fluid
-
Replacing Safety Stickers
-
Replace main hydraulic hoses and fittings
-
Replace start/stop button
-
Replace key switch
-
Key Guard Installation

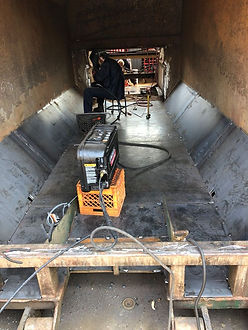